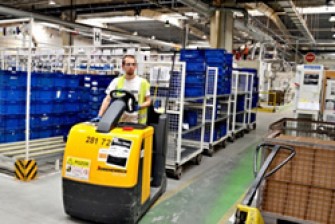
Účinné fungování logistických procesů představuje jeden z předních cílů ve většině společností, které působí v různých průmyslových odvětvích, jako jsou strojírenství, elektrotechnika, automobilový průmysl apod. Pro správnost a kvalitu výrobního procesu je nutností správné rozmístění výrobních strojů, mezioperačních skladů a správné umístění cest pro přísun a odsun materiálu, polotovarů a výrobků. Při distribuci a odvozu materiálu k výrobním strojům se v minulosti používaly různé druhy dopravních prostředků, které byly přivolané pomocí povelu (podle potřeby) v daný čas.
Takový systém zásobování však měl širokou škálu nevýhod, často docházelo ke vzniku prostojů, případně kapacita dopravních prostředků nebyla využívána v dostatečné míře, popřípadě celý systém zásobování fungoval neefektivně. Zjednodušeně řečeno, fungování tohoto systému můžeme přirovnat k taxislužbě, kdy si zavoláme dopravní prostředek v určitou dobu, tj. kdy ho právě potřebujeme, a ten nám odnese nebo přinese materiál v přesném čase. Chyběla zde však přesnější koordinace celého procesu, docházelo k situacím, kdy byl materiál kvůli dřívější objednávce dodán na pracoviště, které ještě mohlo pracovat, a naopak pracoviště, které dodávku potřebovalo, muselo na materiál čekat a přerušit svou činnost. Takto fungující systém zásobování byl tak v konečném důsledku brzdícím faktorem pro zvyšování výrobní kapacity. Z tohoto důvodu se stále více hledaly v různých společnostech způsoby, jak celý proces zásobování zefektivnit.
Inovaci v tomto směru přinesl až systém Milk Run. Jeho fungování je založeno na jednoduchém principu soustavy dopravních prostředků kolujících kolem výrobních strojů a montážních linek s účelem dodání nebo odběru materiálu. Základní myšlenka celého tohoto procesu spočívá v tom, že souprava dopravních prostředků se dostavuje na místo nakládky nebo vykládky v určeném intervalu bez manuálního přivolání. Systém je vázán na časový rozvrh a má předem stanovené trasy a zastávky. Činnost můžeme přirovnat k systému linek MHD ve městě, které jsou provozovány podle přesně stanoveného jízdního řádu.
Charakteristika systému Milk Run
Pojem Milk Run pochází z americké terminologie. Milk Run je pojem spojený s dodávkou plných lahví s mlékem a odběrem lahví prázdných. K této výměně docházelo vždy v pravidelných intervalech každé ráno. V logistice se tento pojem používá od roku 1995, kdy Meusel Winfrid ho přirovnal k okružním jízdám nákladních vozidel.
Systém Milk Run v logistice je spojen s pohybem dopravních prostředků, který slouží k usnadnění při distribuci zboží nebo při jeho shromažďování. Souprava dopravních prostředků má za úkol zásobit po předem naplánované trase definovaný počet odběrných míst s přesným objemem materiálu v určitém časovém okamžiku [0, 1, 2].
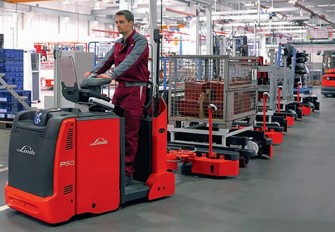
Systém Milk Run jako součást intralogistiky [1, 2]
Po provedení tohoto úkonu se souprava otáčí a vrací zpět do skladu. Cestou zpět sbírá jednotlivé přepravní obaly, případně výrobky a polotovary z pracovišť do skladu. V prvotních fázích využívání tohoto systému byl provozován většinou jako součást mezifiremní dopravy, později si však postupně našel cestu a zdomácněl v rámci vnitropodnikových logistických systémů.
Vybrané technické varianty zásobování výrobních linek
Donedávna byly ve většině průmyslových závodů nosnou kostrou vnitropodnikových logistických systémů paletové nebo vysokozdvižné vozíky. Princip takového zásobování spočíval v distribuci a odvozu materiálu v době, kdy je na to upozornil pracovník daného pracoviště.
Tento druh dopravy měl však celou řadu nevýhod pro fungování v podniku. V první řadě to byla vytíženost vozíků, která byla většinou max. 60 % z celkové doby výroby. V důsledku toho tak často docházelo k nedostatku vozíků, což způsobovalo velké časové zdržení v rámci výroby. Řešením však nebylo ani zvýšení počtu vozíků, protože pak nastala opačná situace, kdy v důsledku nadbytku vozíků nebyla dostatečně využita jejich kapacita a časová náplň. Dalším problémem, se kterým bylo třeba při tomto systému zásobování a dopravy počítat, byly prostorové problémy, které byly omezující pro pohyb zejména pro vysokozdvižné vozíky. Komplikace také způsobovala i skutečnost, že v některých případech nebylo možné přepravovat různé druhy materiálu, stále existovalo vysoké riziko nehody, bylo realizováno mnoho prázdných jízd a v neposlední řadě je třeba zmínit i vysoké náklady na investice a údržbu.
Z uvedených důvodů se postupně některé podniky, které realizovaly především hromadnou sériovou výrobu, začaly přeorientovávat na systém řízení dopravy a zásobování systémem Milk Run.
Takový systém začaly většinou realizovat vlakovou soupravou sestávající z tažného vozidla a několika tažených vozíků (obr. 2). Systém může být ovládán manuálně, kdy v prostoru tažného vozidla sedí obsluha, nebo automaticky pomocí řídících snímačů umístěných v tažném vozidle, které snímají předem naplánovanou trasu vyznačenou na podlaze výrobní haly a současně identifikují případně překážky nacházející se na jeho trase (obr. 3).
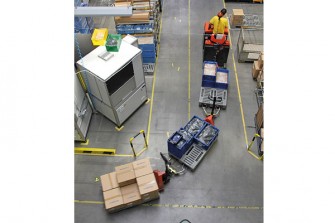
Ukázka možnosti zásobování výrobních linek v rámci výrobní logistiky [3, 4]
Mezi hlavní výhody takto provozovaného systému zásobování (někdy označovaného jako logistický vláček) je to, že jízdy jsou řízeny přesně podle rozvrhu a mají své intervaly příjezdu a odjezdu. V důsledku toho je možné dopravit více druhů materiálu najednou, zvýšila se výrazně kapacita oproti použití vysokozdvižných vozíků. Další výhody spočívají v minimalizaci prázdných jízd, zvýšení bezpečnosti při manipulaci s dopravovaným materiálem, nižších nákladech na investice ve srovnání s vysokozdvižnými vozíky a v neposlední řadě i vysoké pružnosti používaných vozů.
Provozování takové soupravy spočívá v tom, že se pohybuje po vyznačené trase mezi jednotlivými pracovišti. Vyznačení trasy je možné v současnosti realizovat různými způsoby a záleží jen na konkrétním provozovateli, pro který způsob se rozhodne.
Začátek trasy je nejčastěji ve skladu, resp. na místě určeném pro naložení materiálu na soupravu v požadovaném objemu nebo množství. Pak souprava směřuje mezi jednotlivá pracoviště, kde dochází k vykládání požadovaného materiálu a případnému nakládání prázdných přepravních obalů. Další možností je, že po vyložení může probíhat i naložení hotových výrobků. Pokud souprava odbaví všechna pracoviště, směřuje na místo určené pro nakládku. Tento cyklus probíhá podle určitého časového rozvrhu v předem určených intervalech.
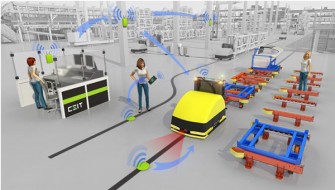
Automatický logistický systém CEIT [5]
Kvůli správnému fungování celého procesu zásobování je třeba jeho odladění a ověření tak, aby v reálném provozu nenastaly žádné vážné komplikace. Jednou z efektivních metod, kterou lze pro tento ověřovací proces použít, je metoda počítačové simulace v programu Tecnomatix Plant Simulation.
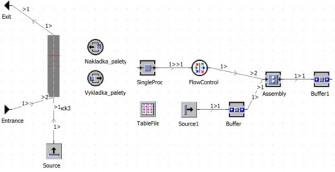
Ukázka části struktury frame reprezentující místo pro vychystávání zboží
Simulace zásobování výrobních linek pomocí programu Tecnomatix Plant Simulations
Možnosti simulace zásobování, jako součásti podnikové logistiky pomocí automatických logistických systémů v rámci Milk Runu, byly řešeny prostřednictvím výzkumu v kooperaci TU Košice a VŠLG v Přerově. V rámci prezentovaného článku bude tato problematika blíže představena na fiktivním montážním pracovišti.
Základní koncepce vytvořeného simulačního modelu je rozdělena do tří základních skupin framů. První skupinu reprezentují framy, ve kterých je simulovaná realizace nakládky, resp. vykládky přepravovaného materiálu (tzv. supermarket). Jejich počet závisí na konkrétních provozních podmínkách. V našem případě jsme kvůli zjednodušení uvažovali pouze s jedním supermarketem, jehož struktura je znázorněna na obr. 4.
Pro simulovaný proces v rámci supermarketu jsme předpokládali jednoduchý proces, ve kterém bude docházet k odebírání prázdných přepravních jednotek z automatického logistického systému a současně na ten samý systém budou nakládány v případě dostupnosti i přepravní jednotky naplněné materiálem. Během popisovaného procesu je však možné podle potřeby uvažovat i s více druhy přepravních jednotek, jejich kapacitou a případně i specializací na konkrétní druh přepravovaného nákladu.
Dále byla v rámci modelu prezentována pouze jedna souprava logistického vláčku, kterou tvořily dva vlečné vozíky a jeden tažný prvek – lokomotiva (obr. 5).
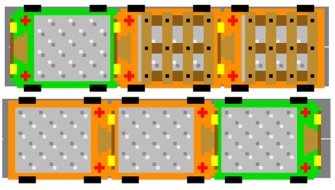
2D vizualizace automatického logistického systému v průběhu simulačního experimentu s nákladem a bez nákladu
V průběhu simulačního experimentu bylo možné sledovat a vyhodnocovat různé ukazatele o provozovaném automatickém logistickém systému, jako jsou např. informace o zdroji energie nebo statistiky jeho časového a kapacitního využití (obr. 6). Lokomotiva měla dále definovanou konstantní rychlost, která se při vjíždění do zatáčky snížila na 65 % původní rychlosti a při výjezdu ze zatáčky se vrátila na původní hodnotu. V případě nasazení více jízdních souprav na jedné trase bylo nutné v simulačním modelu uvažovat s kolizním faktorem, který pomáhal zajišťovat provoz bez rizika vzniku nepříznivé situace. Jeho definování a následná aplikace byla možná díky jeho naprogramování v jazyce SimTalk.
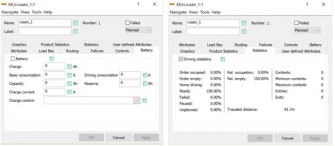
Dialogové okno poskytující informace o zdroji energie a statistiky časového a kapacitního využití lokomotivy logistického vláčku
Každý z tažených vozíků měl definovanou přepravní kapacitu, která mohla být podle potřeby variabilní nebo konstantní, zároveň bylo možné nadefinovat, zda přepravované jednotky lze na jednotlivých vozících stohovat a v jakém počtu.
Nakládka prázdných přepravních jednotek a vykládka přepravních jednotek s nákladem na příslušném pracovišti byla realizována prostřednictvím kombinace senzorů a bloku Transfer Station. V rámci této činnosti byl definován konstantní časový interval, který odpovídal potřebám pro realizaci příslušných manipulačních činností (obr. 7). Problematika přepravních jednotek byla v simulačním modelu podrobněji řešena i z hlediska celkového počtu těch, které se nacházejí v oběhu v průběhu výrobního procesu. Simulační model umožňoval jejich přesnou identifikaci a definování různých kapacit pro přepravu nákladu.
Výsledná vizualizace celého simulačního modelu byla ponechána v základní 2D, resp. 3D podobě, tak jak ji standardně nabízí program Tecnomatix Plant Simulation (obr. 7, 8).

Ukázka části struktury framu reprezentujícího místo pro překládku a zpracování zboží zobrazeného v základní 3D podobě
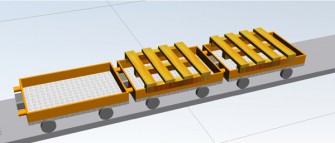
Ukázka základního 3D zobrazení logistického vláčku v simulačním modelu
Možnosti využití customizovaných knihoven
Další možností pro detailnější modelování a simulaci zásobování výrobních linek v rámci vnitropodnikových logistických systémů je používání customizovaných knihoven upravených na míru pro konkrétního uživatele.
Pod pojmem customizovaná knihovna rozumíme speciální knihovnu, která obsahuje velké množství speciálně vytvořených bloků, logicky uspořádaných do funkčních celků podle detailních požadavků příslušného uživatele, přičemž činnost těchto bloků je řízena složitými algoritmy vytvořenými v programovacím jazyce SimTalk.
Jednotlivé nově vytvořené a naprogramované bloky tak nabízejí uživatelsky specifické funkce, které se výrazně liší od základních bloků umístěných v klasických knihovnách programu Tecnomatix Plant Simulation. Ve většině případů je práce s nimi zcela odlišná od běžně zažitých zvyklostí a postupů, které uživatelé základní verze znají a ovládají. Jejich zvládnutí vyžaduje zpočátku delší dobu studia, především struktury jednotlivých bloků programovacího nástroje SimTalk.
Jako příklad můžeme uvést připojení jednotlivých specializovaných bloků k dopravní trase, které se provádí automaticky a na jeho vytvoření postačí obyčejné umístění příslušného bloku k druhému bloku s názvem Track. Celkové připojení se následně realizuje po spuštění simulačního experimentu automaticky, přičemž směr připojení se provádí pomocí zatržení příslušných voleb směru připojení v rámci upraveného dialogového okna příslušného bloku (obr. 9). Samotný bod připojení není na první pohled viditelný, avšak po již zmíněném spuštění simulačního experimentu jeden blok automaticky detekuje blízkost jiného bloku a vytvoří propojení.
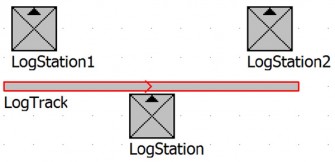
Automatické propojení bloků z customizované knihovny
Každý z bloků customizované knihovny má svou specifickou strukturu, jejíž základní podstata je však pro většinu bloků stejná (obr. 10). Obecně ji tvoří bloky, které je možné rozdělit do tří skupin. První tvoří bloky, v nichž se parametry zadávají přes různé tabulky, druhou skupinu tvoří zase bloky, ve kterých je třeba příkazy přímo programovat, a následně existuje třetí skupina bloků, v nichž jsou zakázány jakékoliv zásahy, protože by ohrozily funkčnost a stabilitu celého systému.
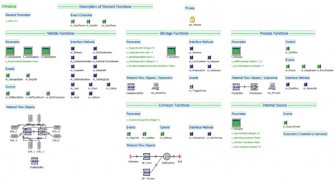
Detailní pohled na strukturu bloku z customizované VDA knihovny určené pro program
Tecnomatix Plant Simulation
Využití takto vytvořených modelů je velmi vysoké a nabízí jejich uživateli širokou škálu možností pro potřeby modelování a simulace. Takovým způsobem je možné vytvořit libovolné bloky, které budou reprezentovat přesně specifické funkce a činnosti. Je však třeba znovu zdůraznit, že vývoj a odladění takto připravených bloků je náročný z časového hlediska a klade vysoké nároky na programátorské schopnosti. Práce s těmito bloky je také, jak již bylo zmíněno, náročná. Benefity z ní jsou však jednoznačné, protože tvorba simulačního modelu se omezuje pouze na jednoduché vložení bloku na pracovní plochu a všechno ostatní je možné naprogramovat pomocí různých příkazů v programovacím jazyce. Odpadá tak složité a zdlouhavé proklikávání jednotlivými bloky, otevírání dialogových oken a rozbalovacích nabídek.
Současně je třeba zmínit, že takto vytvořené bloky a knihovny již nenabízejí takové možnosti vizualizace a grafické úpravy výsledné podoby simulačního modelu. Konkrétně zde většinou chybí podpora 3D grafiky a využívá se jednoduchá, avšak stále plně srozumitelná 2D grafika (obr. 11, 12). Na druhou stranu je však mnohem bohatší nabídka různých grafů a statistických přehledů, které dávají uživateli dokonalý přehled o analyzovaných procesech.
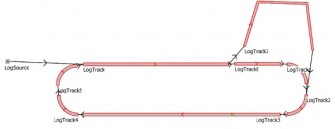
Příklad vytvoření dopravní trasy pomocí nástrojů customizované knihovny
Při detailnějším pohledu na obr. 12 je na první pohled zřejmé, že bloky v customizovaných knihovnách mají úplně jinou vizualizaci jako bloky klasických knihoven programu Tecnomatix Plant Simulation.
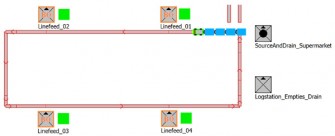
2D vizualizace zásobování pracovišť pomocí logistického vláčku se 4 vagónky
Závěr
Současný trend v oblasti podnikové logistiky v mnoha průmyslových podnicích směřuje k zavádění a rozšiřování různých typů automatizovaných systémů zásobování. Jde o snahu, která je podporována požadavky pro zvyšování spolehlivosti, snižování provozních nákladů, dodržování časových a výrobních harmonogramů. Mezi nejčastější aplikované řešení automatizovaných systémů zásobování patří tzv. logistický vláček.
Použití logistického vláčku v interní logistice umožňuje dosáhnout ve výrobním procesu lepší manipulační výkon a současně zvýšit objem přepravovaného zboží. Zdokonaluje logistický proces tím, že i menší jednotky a kontejnery mohou být dodávány častěji, tok zboží je stálý, následný a pravidelný, čímž se naplňují hlavní principy dnešní výroby: „just-in-time“ a „just-in-sequence“. Díky současné dodávce více kontejnerů s různým materiálem se snižuje intenzita interní přepravy v rámci výrobní haly. Dalšími přidanými hodnotami jsou menší riziko nehod, protože logistický vláček jezdí jednosměrně. Velkou výhodou je i možnost jezdit i v užších uličkách [6].
Ve většině případů znamená pro podnik zavádění logistického vláčku, především v počátečních fázích řešení projektu, významný zásah do původně fungující podnikové koncepce. Pro snížení negativních dopadů a identifikaci případných problémů je možné efektivně využít metodu počítačové simulace.
Metoda počítačové simulace představuje proto v současnosti pro vnitropodnikové logistické systémy důležitý prostředek pro potřeby jejich analýzy a hodnocení. Výsledky simulačních experimentů umožňují získat detailní informace, které se běžným způsobem nedají získat, resp. postřehnout (obr. 13). Z tohoto důvodu je již dnes nepředstavitelné, aby metoda počítačové simulace nebyla v oblasti logistiky používána.
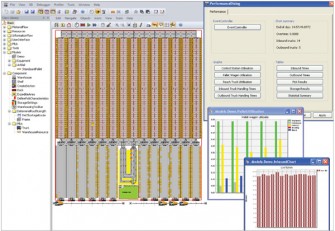
Ukázka výstupů pomocí customizované knihovny [7]
Článek je součástí řešení projektů grantových projektů VEGA 1/0258/14, VEGA 1/0619/15, VEGA 1/0063/16, KEGA 006STU-4/2012 a KEGA 018TUKE-4/2016.
Literatura
- http://www.linde-mh.sk/images/media-info/09-01.jpg
- http://www.linde-mh.sk/images/media-info/09-02.jpg
- http://img.ihned.cz/attachment.php/990/62477990/9E75LGqJKS0yhIwmvz3NUsMixrFt86HB/44-46_Vlacky-2.jpg
- http://www.logisticsatoz.com/wp-content/uploads/Jungheinrich-faurecia-1__460.jpg
- http://ceittechinnovation.eu/agv-mapa/images/agv-systemy0.jpg
- http://www.linde-mh.sk/media-informacie/161-logisticky-vlacik
- http://www.cardsplmsolutions.nl/upload/resources/pdf/plant-simulation-warehousing-and-logistics-5664.pdf
- Čujan, Z. Logistika výrobních technologií. 1. vydání. Vysoká škola logistiky, o. p. s., v Přerově. Přerov, 2013. ISBN 978-80-87179-31 4.