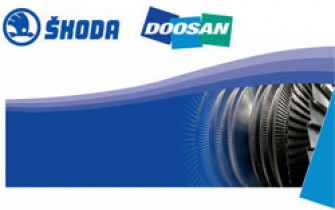
Dnes najdeme ve výrobním programu Škody Power vše od parních turbogenerátorů až po strojovny pro různé aplikace, mezi které patří fosilní a jaderné elektrárny, kogenerace, kombinované cykly, spalovny komunálního odpadu nebo biomasy. Důležité je, že ve všech odvětvích probíhá výzkum a vývoj, přičemž teoretické závěry se ověřují ve vlastní experimentální laboratoři.
Konstrukce
Odbor konstrukce má celkem pět konstrukčních oddělení a oddělení technické podpory. Pod konstrukci spadá 104 kmenových zaměstnanců, včetně 18 v indickém Chennai, a 10 externích zaměstnanců. Před rokem 2003 se podobně jako v jiných strojírenských závodech u nás navrhovalo nejprve na prknech, později ve 2D AutoCADu. První pokusy ve 3D u jednodušších dílů vznikaly v Euclidu a PDMS. Pro výpočty se používaly systémy Systus, Pro/Mechanica a Ansys, pro simulace proudění pak CFD Fluent. Pro správu dat se používá systém CADIM, ale zcela chybí správa obecné a technické dokumentace. Jako návazný ekonomický systém byl využíván Baan IV.
Přechod na PLM
Rok 2003 považují ve firmě Škoda Power za zlomový. Od 4. čtvrtletí roku 2002 začíná probíhat první fáze zavádění CAx – PDM, která je následně v květnu 2005 následována fází doplnění funkčnosti PLM. V první fázi se zavádí 3D CAD Catia V5, včetně vazeb na doposud používané CAx nástroje. Probíhá zavedení a náhrada doposud používaného systému PDM a oddělení jsou vybavena novým hardwarem. V následující druhé fázi je systém PDM doplněn o funkčnosti systému sledování životního cyklu výrobku (PLM). To ale není všechno, protože v podstatě souběžně s druhou fází probíhají fáze 3, 4 a 5. Třetí fáze optimalizuje procesy při návrhu průtočné části turbíny, čtvrtá fáze optimalizuje procesy při návrhu turbínových dílů a pátá fáze se zabývá optimalizací procesů při návrhu kondenzace a regenerace. Pro sledování životního cyklu výrobku bylo zvoleno PLM řešení Eigner PLM s návazností na ERP systém Baan V. Shodou okolností v srpnu 2003 kupuje firmu Eigner společnost Agile a tu pak v červnu 2007 společnost Oracle. Dnes tedy je jako PLM řešení využíváno Oracle Agile e6.
Jako implementátor, poskytovatel podpory a servisu vystupuje v celém projektu společnost Technodat a od roku 2006 z ní odštěpená plzeňská společnost TD-IS.
Identický model pro Drawing, FEM a technologii
Několik otázek a odpovědí
Na to, jak nejlépe postupovat při zavádění PLM, jsme se zeptali pracovníka firmy Škoda Power, Ing. Davida Brušáka, vedoucího oddělení konstrukce KOIV.
Z předchozího článku se možná zdá, že zavést PLM řešení není žádný problém. Ale tak tomu asi není, že?
Ano, to máte určitě pravdu. Jsou známy případy, kdy se firmy se zaváděním PLM potýkaly roky či od zavedení nakonec zcela upustily. U nás tento proces proběhl, řekl bych, skoro až učebnicově a z výše uvedeného to může budit dojem, že je to proces celkem jednoduchý a dobře zmapovaný. Úspěšná implementace PLM je dána ale spoustou faktorů, které lze či nelze zcela ovlivnit, resp. se na ně připravit, ale k tomu se určitě dostaneme v dalších otázkách.
Co potřebuje firma, která chce zavést PLM ve vaší konfiguraci?
Pevné nervy. No teď to trochu zlehčuji, ale i tento bod určitě ke zvládnutí celého procesu patří. V první řadě musí firma vědět, co a proč chce, a mít vůli dotáhnout celý proces do konce. V tom určitě velkou roli sehrává druhý důležitý faktor a tím je schopný a zkušený implementátor, který může v tomto směru podat pomocnou ruku a vést celý projekt správným směrem, nastavit milníky a cíle projektu a pomoci s překonáním problémů během implementace. Škoda Power si jako implementátora zvolila firmu Technodat. Toto jsou určitě takové ty základní pilíře, ale nezaručují úspěšnou realizaci. Té se nám podařilo dosáhnout hlavně díky takzvaným klíčovým uživatelům, což byla skupina většinou mladších a dost často začínajících konstruktérů s minimální praxí, ale s obrovským nasazením a dobrým základem obecných znalostí zejména na poli 3D CAD a částečně i PLM. Nevím, zda to bylo dáno opravdu dobrou volbou našeho tehdejšího vedení při náboru těchto lidí, nebo se nějakou náhodou povedlo dát dohromady tým lidí opravdu zapálených pro věc a ochotných investovat svoje znalosti a schopnosti do tohoto projektu nad rámec jejich standardních povinností. Musím říci, že tito klíčoví uživatelé sehráli hlavní úlohu při implementaci. Byli to lidé, kteří jednak samozřejmě museli mít výsledky dle stanovených plánů implementace, ale zároveň byli schopni přenášet, nastavovat a vysvětlovat procesy ostatním konstruktérům s určitým pedagogickým taktem tak, aby tyto novinky byly přijímány pozitivně. Zároveň byli schopni proniknout do jednotlivých vazeb napříč útvary a hledat a vytvářet funkční řešení tak, aby byla uživatelsky přívětivá a použitelná. Klíčoví uživatelé byli ti, kteří se snažili maximálně ulehčit přechod z „prkna" či nějakého 2D CAD na velký 3D CAD systém, prakticky ukazovali koncovým uživatelům výhody nového řešení, individuálně s nimi řešili jejich problémy a snažili se jim maximálně ulehčit a zpříjemnit jejich práci. Vedení mělo celkem oprávněný strach, že tyto změny mohou být přijímány negativně, ale mohu s klidným svědomím říci, že díky skupině klíčových uživatelů se povedlo přenést výhody velkého 3D CAD a opravdu uživatelům zjednodušit a zpříjemnit jejich práci. Klíčoví uživatelé byli takovým pojítkem a komunikačním mostem mezi managementem a koncovými uživateli. Klíčoví uživatelé si byli vědomi, že nemají tak obrovské zkušenosti jako stávající pracovníci, a ani se jim v tom nesnažili vyrovnat, spíš se snažili od nich čerpat jejich znalosti a dostávat se do problematiky konstrukce parních turbín a na oplátku jim předávali své znalosti v oblasti CAD a PLM. Tahle symbióza měla i přímou podporu vedení, které stálo za rozhodnutím klíčových uživatelů. Zároveň i klíčoví uživatelé věděli, že vedení si stojí za svým rozhodnutím a nebude v případě nějakého problému hledat nějaká náhradní řešení či ustupovat ze stanovených cílů. Vedení rovněž poskytlo veškeré potřebné prostředky pro to, aby celý proces proběhl efektivně, rychle a bez ohrožení stávající zakázkové náplně.
Jak vybrat dobrého implementátora?
To je trochu záludná otázka. Technodat v době, kdy probíhala implementace u nás ve Škoda Power, již nějaké zkušenosti s implementací sice měl, ale projekt u nás byl poněkud větší a rozsáhlejší a bylo to, nejen pro Technodat, ale i pro další firmy, něco nové a ne zcela zmapované. Proces implementace pak spočíval v tom, že jsme si vzájemně předávali informace, znalosti a zkušenosti a díky velmi dobré vzájemné komunikaci jsme se od sebe hodně naučili a povedlo se nám celý proces celkem bez větších problémů zvládnout.
V té době jsme určitě hledali implementátora, který má dobré reference, zkušenosti a znalosti. Na rozdíl od současnosti ale takových společností příliš nebylo. S firmou Technodat jsme již nějakou dobu spolupracovali a věděli jsme, co od sebe vzájemně můžeme očekávat. To byl i jeden z důvodů, proč volba padla na ně. V současné době, a myslím si, že i díky nám, již mají velmi dobré zkušenosti s implementací a můžeme o nich hovořit jako o dobrém implementátorovi. Pokud bychom nyní hledali dobrého implementátora, určitě bychom se dívali po referencích a zkušenostech v obdobném rozsahu implementace. Pokud firma chce implementovat nějaké PLM řešení, měla by věnovat i pozornost přístupu implementátora, zda je ochoten naslouchat potřebám firmy, či bude tlačit svůj zajetý systém bez ohledu na potřeby firmy. Tím ale samozřejmě nechci říci, že implementátor musí PLM řešení udělat 1:1 ke stávajícím procesům ve firmě, to by určitě nebylo správné, protože zavedení nějakého PLM řešení či obecně zavádění něčeho nového dává prostor ke zmapování, zefektivnění či optimalizaci stávajících procesů, o kterých již dost často ani nikdo neví, proč fungují tak, jak fungují, a právě nadhled implementátora dává možnost vidět to, co lidé v systému již nevidí, a tím celý systém zas posunout někam dál.
Co jste museli nutně udělat a co naopak potřeba dělat nebylo?
Bylo nutné projít nejrůznější procesy a vazby mezi jednotlivými útvary společnosti, zmapovat je a zamyslet se nad jejich smyslem a fungováním, popřípadě najít nějaké nové efektivnější řešení. Jako příklad mohu uvést číslování výkresů. Zažitý způsob spočíval ve vyzvednutí čísla z papírové knihy v jednom oddělení, číslo reprezentovalo formát výkresu. Byly zde snahy zakomponovat do tohoto čísla co nejvíce informací. Z pohledu zpět jsem rád, že se tyto snahy povedlo zastavit a číslo nám na tlačítko generuje samotný PLM systém, je to číslo, které nic neříká o velikosti výkresu, příslušnosti k té či oné sestavě či zakázce. Je to prostě číslo, které generuje systém, a nic víc. Všechny potřebné informace o výkresu, resp. položce jsou obsaženy přímo v PLM včetně všech vazeb na materiál, technologický postup, program kontrol a zkoušek atd. a samozřejmě PLM má k danému číslu výkresu veškerou specifikaci, co se týče rozměru, měřítka, hmotnosti atd.
Stejně tak se povedlo nahradit veškeré ruční podpisy na výkresech „elektronickým podpisem v PLM", který se přenáší do rohového razítka výkresu. Dříve konstruktér obíhal polovinu společnosti a nechával si výkres ručně podepisovat a ten se následně skenoval zpět do systému. Nyní v PLM systému máme u položky vidět celou její historii, kdy vidíme, kdo ji kresli, měnil, kontroloval, kdo posuzoval technologičnost či nakupitelnost či kdo položku schválil, samozřejmě včetně změnového řízení. Všechny tyto informace se pak přenášejí do rohového razítka a veškeré obíhání je řešeno pomocí WorkFlow přímo v PLM. Spuštění tohoto procesu bylo velkou úlevou pro konstruktéry, kterým odpadl zdlouhavý proces fyzického obíhání jednotlivých pracovníků a dožadování se podpisů.
Podobných věcí by se našla celá řada, ale myslím si, že nemáme prostor je jmenovat všechny. Ještě se zmíním o jedné věci, a tou je klasifikace. Je to velmi silný nástroj PLM. Naší původní vizí byla plná klasifikace všech dílů. S ohledem na tvarovou složitost některých komponent a jejich možnost následného využití jsme se nakonec omezili jen na vybrané díly, které z našeho pohledu mají smysl a jsou zaklasifikovatelné tak, aby to bylo přínosné a nestrávili jsme zbytečně čas plnou klasifikací dílů, které také již nikdy nemusíme použít. Jednotlivé díly jsou samozřejmě i bez klasifikace dohledatelné ať už přes vazbu v zakázce nebo přes unifikované názvosloví, které částečně řeší funkci klasifikace.
Co je výhodnější, pracovat ve 2D, nebo ve 3D?
Tak tady je otázka zcela jednoduchá. Pokud mohu něco udělat ve 3D, určitě se vyplatí do toho jít. Přínos 3D je zcela nepopíratelný a myslím si, že asi není nutné to tu víc rozebírat, na toto téma bylo napsáno již hodně. Navíc pokud mám nějaký z větších 3D CADů a mohu využívat jejich funkčností jako u nás například generické modely, pak opravdu není co řešit. Vzhůru do 3D.
Co znamenají generické modely a jak je využívat?
Generické modely jsou speciální modely, většinou řízené pomocí tabulky v MS Excelu, která může provádět nejrůznější výpočty, kontroly, popř. uchovávat jakési know-how z dané oblasti a řídit tvorbu modelu. U nás máme vytvořeno několik takovýchto modelů. Jako jeden z příkladů uvedu generické rozváděcí kolo. To je model, který umí řešit velice jednoduše na několik kliknutí myší tisíce nejrůznějších tvarových modifikací pro jeden z klíčových dílů parní turbíny. Na základě vyplnění tabulky v MS Excelu konstruktér během velice krátké doby je schopen vytvořit kompletní dokumentaci k tomuto dílu. Před zavedením tohoto modelu trvalo vytvoření rozváděcího kola 90 konstrukčních hodin. Nyní je to cca 30 hodin – typicky se jedná o jeden výkres a model sestavy (sestava o cca 10 typech dílů ve vícenásobných reprezentacích), 3 výkresy a modely komponent. V uvedeném čase se provede kompletní tvorba, uložení do PLM a kontrola od zkušenějšího konstruktéra. Velice jednoduchý způsob snížení konstrukčních hodin s celkem zanedbatelnou počáteční investicí. I zde platí, stejně jako u přechodu z 2D do 3D, nebát se a neříkat od začátku „To nejde". Možnosti 3D jsou velké a z vlastní zkušenosti víme, že o komponentě, o které jsme si dlouho mysleli, že není možné ji zparametrizovat, a parametrizovali jsme jen její dílčí části, jsme schopni nakonec všechny tyto dílčí součásti propojit a vytvořit generický model původně neparametrizovatelného dílu.
Co znamenalo zavedení PLM řešení pro Škoda Power? Jaké konkrétní důsledky mělo a má v současnosti?
Z literatury a nejrůznějších článků jsou známy nejrůznější hodnoty zkrácení průběžných dob tvorby výrobku. Jen pokud uvedu generické modely nebo například změnu obíhání firmy s výkresem v ruce kvůli podpisům, řešení pomocí WorkFlow v PLM systému ukazuje, že došlo k výraznému zkrácení průběžných dob a zvýšení průtočnosti zakázek firmou, a to ve velmi krátkém čase. Nebudu zde říkat nějakou konkrétní hodnotu, ale ty úspory jsou značné v porovnání s investicemi do implementace. V současnosti se na konstrukci hrne větší a větší množství práce, takže stále hledáme další a další způsoby, jak si práci ulehčit, zkrátit průběžné doby a přitom snížit riziko vzniku neshod. Bez PLM a 3D CAD bychom měli prostor pro tyto aktivity velice omezený a jen díky těmto pokročilým nástrojům jsme schopni zvládat nároky na nás kladené a být úspěšnou firmou, která je schopna plnit požadavky zákazníků v požadované kvalitě a v požadovaném čase. Což jsou dva faktory, které se stále více sledují a ovlivňují šance na získání projektu.
Jaké inženýrské systémy v současnosti využíváte?
V nedávné době jsme začali testovat od dodavatele Catia V5 software 3DVIAComposer a pro komunikaci s indickou kanceláří používáme redlining pro výměnu a kontrolu dokumentace v softwaru AutoVue.
Využíváte také 3DVIA Composer. Jaký největší přínos vám zavedení tohoto softwaru přineslo?
Původně jsme viděli v tomto softwaru jakousi obdobu 3D CADu, kterou bychom rádi používali pro náčrtky, dokumentaci atd. Naštěstí jsme se od tohoto názoru oprostili a objevili jsme kouzlo tohoto softwaru, který kromě toho, že pracuje 3D daty, nemá s CAD nic moc společného. Je to ale úžasný nástroj, kde se celkem jednoduše dají připravovat nejrůznější obrázky, ať už jako podklady pro manuály a návody nebo jako manažerské výstupy pro prezentace či reklamní účely. Tvorba podobných obrázků v Catia V5 je sice možná, ale 3DVIAComposer to dělá výrazně rychleji, jednodušeji a elegantněji, přičemž výsledky jsou na velmi vysoké úrovni. Díky tomuto nástroji jsou některé návody, které jsme složitě vytvářeli a popisovali, nahrazovány obrázkovými postupy či dokonce animacemi a jsou pro naše zákazníky uživatelsky příjemnější, jednodušší a zajímavější. Dokonce i tento nástroj je schopen šetřit nemalé náklady. Naši dokumentaci předáváme nejrůznějším zákazníkům a dost často je nutné ji provádět v jejich rodném jazyce. Díky bohatší obrazové dokumentaci jsme výrazně snížili požadavky na překlady a někdy je dokonce zcela odbourali.